Blog
A Simple Guide to AGV & AMR Charging
2025-06-30 | Calvin
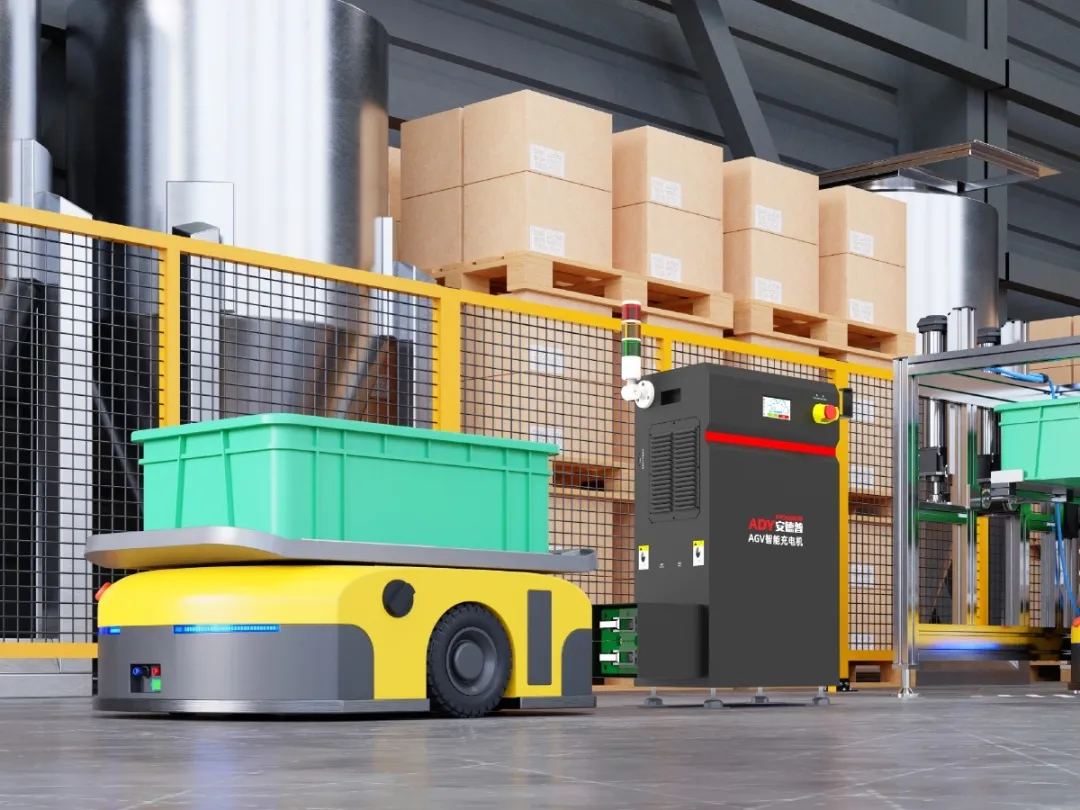
In the era of Industry 4.0 and the rapid development of smart manufacturing, Automated Guided Vehicles (AGVs) and Autonomous Mobile Robots (AMRs) have become pivotal players in modern factories and logistics warehouses. For AGV and AMR charging solutions, LiFePO4 Battery Shop offers four types of intelligent chargers: the side-contact telescopic charger, floor-mounted charger, plug-in charger, and wireless charger. With their unique technological principles and application scenarios, these chargers collectively form a diversified AGV/AMR charging solution.
01 Side Charging – The Space-Saving Flexible Option
The side-contact telescopic charger comes in integrated and split types, with a power range of 3-20KW. It operates based on side-contact technology—when an AGV docks at the designated position, the contacts align precisely to establish an electrical pathway, enabling power transfer. This solution is suitable for automated charging of AGV unmanned forklifts, tow tractors, and other autonomous robots. The advantages of this charging method include high automation (requiring no manual intervention), high conversion efficiency, and customizable charging parameters such as capacity. It ensures an efficient and stable charging process, meeting the power requirements of AGVs with varying power needs.
02 Floor Charging – The Dedicated Solution for Clean Environments
The floor-mounted charger consists of a main unit and brush plates/blocks, with a power range of 3-20KW and compatibility with 24V/48V/80V/96V voltage platforms. When an AGV arrives at the charging station, the brush block makes contact with the brush plate, forming a conductive pathway to charge the AGV. This product is suitable for automated charging applications such as warehouse shuttle AGVs, overhead shuttle robots, food delivery robots, patrol robots, and cleaning robots.
03 Plug-in Charging – The Standard Solution for Fast and Precise Charging
The plug-in charger, also known as the AMR smart charger, has a power range of 3-6KW. Charging is accomplished by plugging the charging connector on the AMR into the socket of the fixed charger. When the AMR's battery runs low, the scheduling system directs it to the charger, where a mechanical or automated docking mechanism precisely inserts the plug into the socket to establish an electrical connection. The alignment tolerance ranges are: -50mm backward, ±20mm left/right, ±7mm up/down, and a 1° tilt angle. This method features a clear and reliable charging interface and is suitable for automated charging of unmanned forklifts, sorting robots, and lifting robots.
04 Wireless Charging – The Ultimate Flexible Solution of the Future
AGV wireless charging technology is based on magnetic resonance principles. The wireless charging system consists of two main components: the transmitter and the receiver. The receiver is installed on the AGV's underside, while the transmitter is placed in the designated charging area to enable wireless power transfer. The biggest advantage of wireless charging is its flexibility, with a charging distance range of 15-40mm. It also supports multi-device charging—a single wireless transmitter can be matched with robots of different voltages, types, and functionalities, achieving compatibility across multiple models, communication protocols, and battery types. This makes it ideal for automated charging in harsh environments such as high-explosion-risk or high-dust conditions, applicable to inspection robots, unmanned forklifts, and AGV carts.
AGV/AMR smart chargers effectively ensure continuous and stable operation of robots, with the intelligent scheduling system playing a critical role. It monitors the battery levels of each AGV in real time. Once the battery level falls below a set threshold, the system intelligently dispatches the AGV to an available charger based on factors such as task urgency, remaining battery level, and charger availability. This ensures priority handling of urgent tasks, prevents "power competition," significantly improves operational efficiency, and reduces overall operating costs.
Different AGV/AMR charging methods have distinct technical characteristics and applicable scenarios. When selecting a solution, enterprises must consider factors such as the production environment, charging efficiency requirements, and budget constraints to build a more efficient and cost-effective energy management system. In the future, AGV charging technology will continue to evolve, advancing toward greater intelligence and efficiency. "Seamless charging" is expected to become mainstream, providing stronger support for the development of smart manufacturing and intelligent logistics.
- Next:Six Major Trends in Future Industrial Charging Technology
- Previous:Understanding and Preventing Swollen LiFePO4 Batteries: A Comprehensive Guide
Contact Details
Lithium LiFePO4 Batteries and Lithium LiFePO4 Cells Supplier - LiFePO4 Battery Shop
Contact Person: Miss. Elena Wang
WhatsApp : +8615263269227
Skype : +8615263269227
WeChat :15263269227
Email : info@lifepo4batteryshop.com
All Products
- CALB Battery (0)
- Cylindrical Cell (1)
- Energy Storage System (0)
- Battery Management System (0)
- Sodium ion Battery Cell (0)
- Lithium Titanate Battery (0)
- Ternary Lithium Battery Cell (0)
- REPT Battery (2)
- BYD Battery (2)
- CATL Battery (1)
- Thunder Sky Winston Battery (13)
- EVE Battery (26)
- LiFePO4 Battery Cell (2)
Certification
Customer Reviews
- I have fond memories of our meeting in Shanghai with LiFePO4 Battery Shop Elena. Your company left a strong impression on me with its impressive growth and professionalism. We both value straightforwardness and honesty, which I believe are the most important qualities in any partnership. I am confident that we can build a successful collaboration based on these shared values. —— Robert from USA
- I've been working with LiFePO4 Battery Shop for years, and their reliability is unmatched. While other suppliers frequently change sales teams, LiFePO4 Battery Shop has consistently provided exceptional service with a stable team. Their commitment to quality and customer support truly sets them apart. —— Henry from Australia